在新能源汽车渗透率突破40%的2025年,中国动力电池退役量已突破80万吨,相当于每小时产生9吨“城市矿山”。绿捷锂电池处理设备以“带电破碎+梯度热解+智能分选”为核心技术,构建起覆盖软包、圆柱、方形电池的全品类回收体系,推动锂电池从“环境风险”向“资源宝藏”的价值跃迁。本文从技术架构、应用场景、经济环保效益三方面,解析这场绿色革命的底层逻辑。
一、技术架构解析:从物理拆解到分子级分离的创新突破
绿捷设备通过模块化设计实现全品类电池处理,其核心技术架构包含四大创新维度:
1. 带电破碎系统
氮气密闭环境:氧含量控制在1.5%以下,直接处理未放电电池,突破传统工艺需96小时放电的瓶颈,效率提升50%;
智能撕碎技术:双轴撕碎机配备重型飞轮与水冷轴盒,将电池破碎至30mm以下,单台设备年处理量达1.5万吨,适应软包、圆柱等复杂形态。
2. 梯度热解工艺
低温段(100-200℃):挥发电解液并冷凝回收NMP溶剂(回收率99.2%),同步分解有机粘结剂;
中温段(400-600℃):碳化隔膜与石墨负极,分离极片与铜铝集流体;
高温段(600-750℃):针对三元电池,采用氢气还原技术,使锂、钴、镍迁移至表面,回收率分别达98.7%、99.1%、98.9%。
3. 智能分选矩阵
多级分选技术:磁选分离铁磁性杂质,涡电流分选铜铝金属,气流分选隔膜与黑粉,AI视觉识别系统剔除异物;
黑粉提纯工艺:通过振动筛与旋振分级,将锂电黑粉纯度提升至99.5%,铜铝杂质含量低于0.3%。
4. 环保闭环设计 :废气处理系统:RTO蓄热燃烧+活性炭吸附,VOCs去除率99.5%,粉尘排放浓度<5mg/m3;
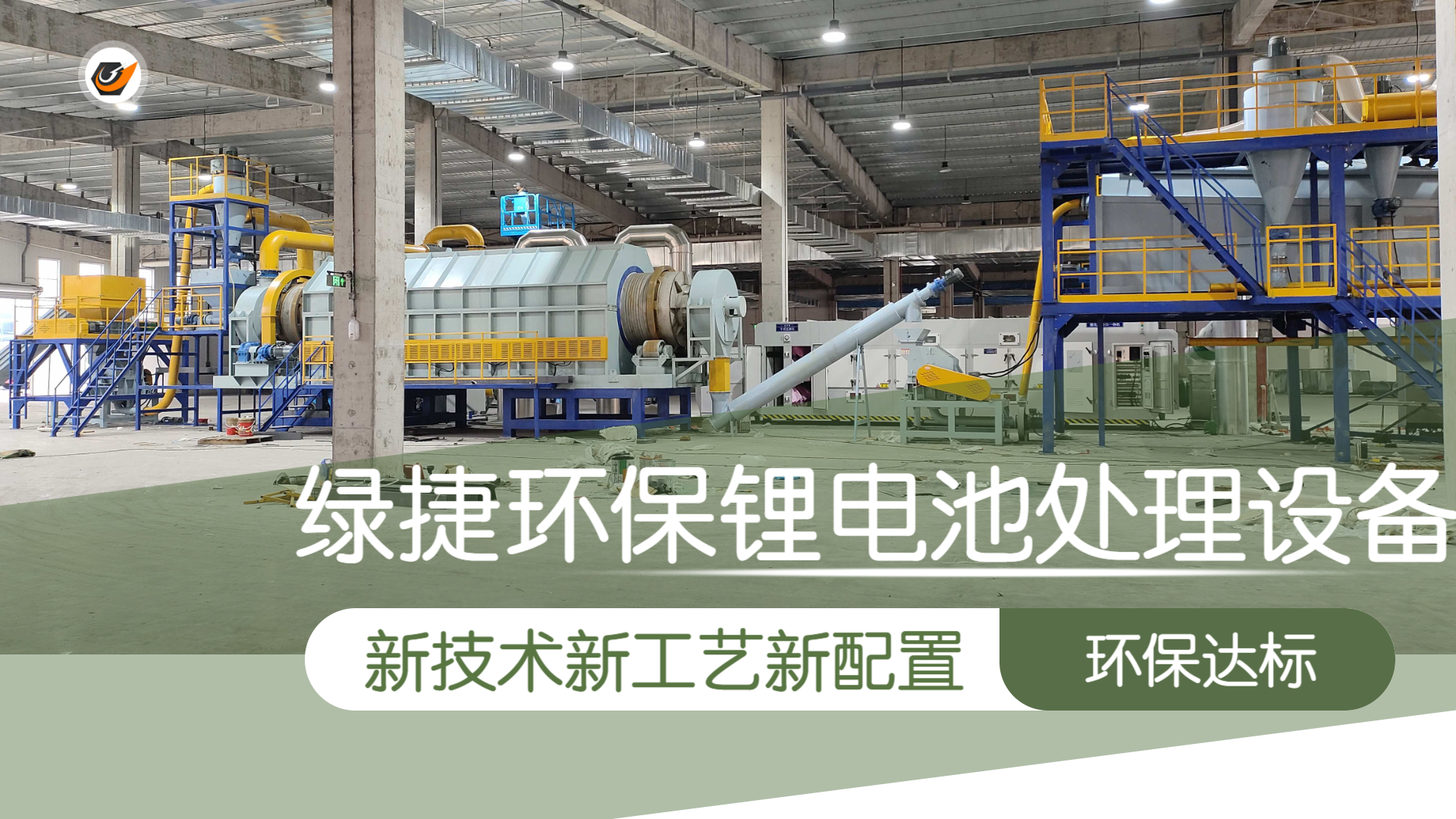
二、多场景应用验证:从实验室到全球市场的规模化落地
绿捷锂电池破碎分选设备已在全球多类型电池回收中实现技术验证,数据表现如下:
1. 软包电池回收
案例:江西某软包电池回收基地(年处理3万吨)
成果:铜回收率98.5%(纯度99.4%),铝回收率95.1%(纯度99.1%),黑粉回收率98.3%(锂含量2.4%);
经济性:单吨处理成本1500元,再生材料直供宁德时代,单吨收益提升120万元。
2. 圆柱电池回收
案例:马来西亚圆柱电池回收项目(年处理2万吨)
成果:钴回收率98.7%,镍回收率99.1%,碳排放降低1.8万吨/万吨电池;
环保性:尾气处理符合欧盟RoHS标准,粉尘回收率99.8%。
3. 磷酸铁锂电池回收
案例:江苏磷酸铁锂电池回收线(年处理5万吨)
成果:黑粉中磷酸铁含量92.3%,锂含量0.5%,再生材料用于储能电池生产;
成本优势:处理成本较传统工艺降低40%,单吨收益增加80万元。
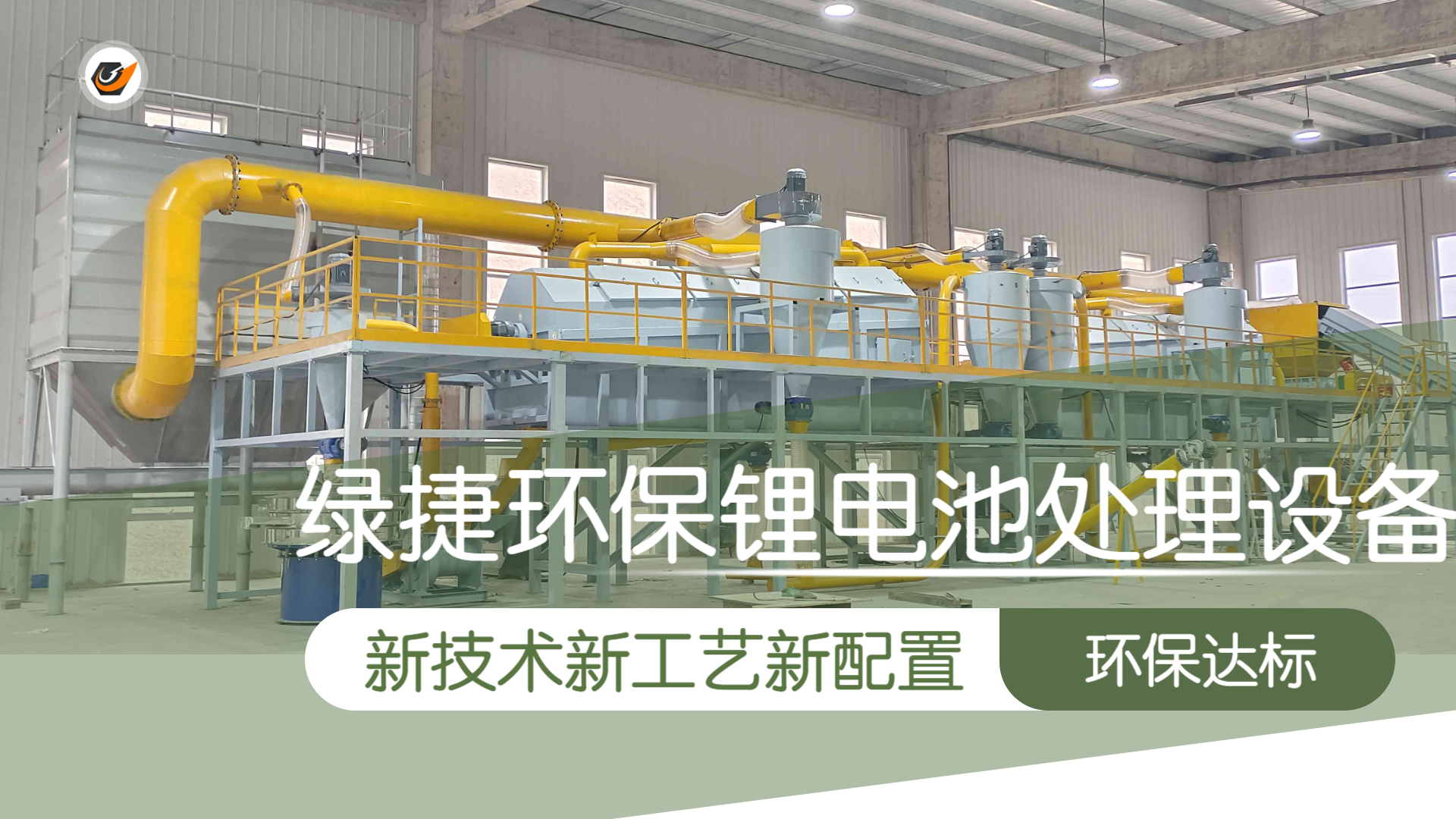
三、绿色经济价值:重构资源循环与碳中和路径
绿捷技术不仅实现资源再生,更推动新能源产业向“零碳闭环”转型:
1. 资源再生效率
每万吨电池处理可回收锂盐300吨、钴12吨、镍20吨,相当于减少原生矿开采面积200公顷;
铜铝再生材料可替代60%的原生金属需求,降低供应链成本30%。
2. 碳减排效益
单吨电池处理减少二氧化碳排放1.5吨,每万吨处理量相当于种植80万棵成年乔木;
热解工艺热能回收率达80%,能耗较传统焚烧降低60%。
3. 经济增值模型
成本端:模块化设计支持1-5万吨/年灵活配置,投资成本降低40%;
收益端:高纯度金属直供头部电池厂商,溢价空间提升20%-30%;
政策红利:入选工信部“白名单”企业,享受税收优惠与财政补贴。
绿捷锂电池处理设备以技术创新重构了废旧电池的价值链,将“城市矿山”转化为新能源产业的可持续资源。其技术突破与产业实践不仅解决了环境隐患,更推动全球锂电池回收行业向高值化、低碳化方向转型。随着2030年全球动力电池退役量突破4246万吨,绿捷的绿色闭环技术将成为实现“双碳”目标的核心动能,为人类可持续发展提供可复制的中国方案。